中溫蠟的收縮率對(duì)鑄件精度有何影響?
發(fā)布日期:2025-05-13 00:00 來(lái)源://sdtxblg.com 點(diǎn)擊:
中溫蠟的收縮率是影響鑄件精度的核心因素之一,其對(duì)鑄件尺寸、形狀及表面質(zhì)量的影響貫穿整個(gè)失蠟鑄造流程。以下從收縮機(jī)制、具體影響及控制策略展開分析:
一、收縮率的形成機(jī)制與類型
中溫蠟的收縮主要源于熱收縮和相變收縮:
熱收縮:蠟料從加工溫度(如70℃)冷卻至室溫(如20℃)時(shí),因熱脹冷縮效應(yīng)產(chǎn)生體積收縮。例如,石蠟基中溫蠟的線收縮率通常為0.8%~1.2%,合成蠟基材料可能更高(可達(dá)1.5%)。
相變收縮:蠟料從液態(tài)凝固為固態(tài)時(shí),分子排列致密化導(dǎo)致體積進(jìn)一步收縮(占總收縮量的30%~50%)。
收縮過程具有階段性:
液態(tài)冷卻階段(加工溫度→凝固點(diǎn)):以熱收縮為主,速度較快;
固態(tài)冷卻階段(凝固點(diǎn)→室溫):熱收縮與相變收縮疊加,收縮量占比約60%~70%。
二、對(duì)鑄件精度的具體影響
1.尺寸偏差
線性收縮:蠟?zāi)5木€收縮率直接決定鑄件的終尺寸。若蠟?zāi)J湛s率未準(zhǔn)確計(jì)算,鑄件可能出現(xiàn)整體尺寸偏小(如蠟?zāi)J湛s率預(yù)估為1.0%,實(shí)際為1.2%時(shí),鑄件關(guān)鍵尺寸偏差可達(dá)0.2%)。
不均勻收縮:
壁厚差異:厚壁區(qū)域冷卻慢,收縮量大于薄壁(如壁厚5mm的蠟?zāi)^(qū)域收縮率比壁厚2mm區(qū)域高0.3%~0.5%),導(dǎo)致鑄件壁厚不均。
結(jié)構(gòu)復(fù)雜度:復(fù)雜件因冷卻路徑不一致,易出現(xiàn)局部收縮異常(如凸臺(tái)、筋板處收縮率比平面高0.1%~0.2%)。
2.形狀畸變
應(yīng)力集中:蠟?zāi)@鋮s時(shí)若內(nèi)部應(yīng)力釋放不均,可能產(chǎn)生彎曲、扭曲等變形。例如,長(zhǎng)條形蠟?zāi)#ㄈ巛S類)若兩側(cè)冷卻速度不一致,可能向冷卻慢的一側(cè)彎曲,導(dǎo)致鑄件直線度超差。
分型面錯(cuò)位:收縮應(yīng)力可能導(dǎo)致壓型(模具)分型面處蠟料位移,形成飛邊或尺寸錯(cuò)位(如分型面處尺寸偏差±0.1mm)。
3.表面缺陷
縮孔與凹陷:蠟料收縮未能及時(shí)補(bǔ)料時(shí),厚壁中心或筋板根部易形成縮孔(直徑0.5~2mm)或表面凹陷,鑄件對(duì)應(yīng)位置會(huì)殘留孔洞或不平整。
冷隔與流痕:收縮導(dǎo)致蠟料流動(dòng)末端補(bǔ)縮不足,可能產(chǎn)生冷隔(線條狀未融合痕跡),影響鑄件表面光潔度。
三、收縮率的控制策略
1.蠟料配方優(yōu)化
添加填料:加入微粉蠟、滑石粉等填料(占比5%~10%)可降低收縮率。例如,含10%滑石粉的中溫蠟線收縮率可從1.2%降至0.9%。
選用低收縮基料:合成蠟(如聚乙烯蠟)比石蠟收縮率低(石蠟基1.0%~1.5%vs合成蠟基0.6%~1.0%),適合高精度鑄件。
2.工藝參數(shù)調(diào)整
控制冷卻速度:
快速冷卻:通過低溫壓型(如金屬模通冷卻水至20℃)或噴霧冷卻,縮短液態(tài)停留時(shí)間,減少熱收縮(線收縮率可降低0.1%~0.3%)。
緩慢冷卻:對(duì)于復(fù)雜件,采用恒溫冷卻箱(如40℃保溫2小時(shí)),使蠟料均勻收縮,減少應(yīng)力變形。
優(yōu)化壓注工藝:
提高壓力:從0.3MPa增至0.5MPa,可通過外力補(bǔ)縮減少收縮缺陷(尤其適用于厚壁件)。
分段壓注:先低壓(0.2MPa)填充型腔,再高壓(0.6MPa)保壓補(bǔ)縮,降低縮孔風(fēng)險(xiǎn)。
3.模具設(shè)計(jì)補(bǔ)償
收縮率預(yù)留:根據(jù)蠟料實(shí)測(cè)收縮率,在模具設(shè)計(jì)時(shí)放大尺寸。例如,若蠟?zāi)J湛s率為1.1%,模具尺寸需比鑄件名義尺寸大1.1%(如鑄件要求φ50mm,模具型腔設(shè)計(jì)為φ50.55mm)。
結(jié)構(gòu)改良:
在厚壁處設(shè)計(jì)工藝?yán)呋驕p薄區(qū),平衡冷卻速度;
復(fù)雜件采用組合式壓型,避免單一模具因收縮應(yīng)力導(dǎo)致變形。
4.過程監(jiān)控與修正
首件檢測(cè):通過三坐標(biāo)測(cè)量?jī)x檢測(cè)蠟?zāi)jP(guān)鍵尺寸,對(duì)比理論收縮率,及時(shí)修正模具或工藝參數(shù)(如發(fā)現(xiàn)某尺寸收縮率比預(yù)期高0.2%,下次生產(chǎn)時(shí)模具相應(yīng)部位放大0.2%)。
批次跟蹤:不同批次蠟料收縮率可能波動(dòng)(如±0.1%),投產(chǎn)前需通過試模確認(rèn)實(shí)際收縮數(shù)據(jù)。
四、典型案例分析
案例1:航空葉片蠟?zāi)W冃?br /> 問題:葉片蠟?zāi)>壈逄幨湛s變形,導(dǎo)致鑄件緣板厚度偏差超±0.05mm。
原因:緣板厚2.5mm,葉身厚1.2mm,冷卻速度差異導(dǎo)致應(yīng)力集中。
解決:壓型緣板區(qū)域嵌入銅質(zhì)冷卻塊(導(dǎo)熱率提高3倍),使緣板與葉身冷卻速度接近,收縮率差異從0.4%降至0.1%,鑄件精度達(dá)標(biāo)。
案例2:齒輪箱蠟?zāi)?s孔
問題:蠟?zāi)]S承座孔內(nèi)出現(xiàn)φ1mm縮孔,鑄件機(jī)加工后暴露。
原因:軸承座孔壁厚8mm,蠟料收縮時(shí)補(bǔ)料不足。
解決:壓注時(shí)增加頂針補(bǔ)料機(jī)構(gòu)(在孔中心設(shè)置可移動(dòng)頂針,冷卻過程中持續(xù)注入熱蠟料),縮孔消除,鑄件合格率從75%提升至98%。
中溫蠟收縮率對(duì)鑄件精度的影響具有累積性和隱蔽性,需從蠟料選擇、工藝設(shè)計(jì)到生產(chǎn)監(jiān)控全流程管控。通過精確測(cè)量收縮率數(shù)據(jù)(建議每批次蠟料實(shí)測(cè)3組以上)、模具動(dòng)態(tài)補(bǔ)償及冷卻路徑優(yōu)化,可將收縮導(dǎo)致的尺寸偏差控制在±0.03mm以內(nèi),滿足航空航天、精密機(jī)械等高精度鑄件需求。實(shí)際生產(chǎn)中,建議建立“蠟料收縮率-工藝參數(shù)-鑄件精度”關(guān)聯(lián)數(shù)據(jù)庫(kù),實(shí)現(xiàn)快速工藝匹配與問題追溯。
一、收縮率的形成機(jī)制與類型
中溫蠟的收縮主要源于熱收縮和相變收縮:
熱收縮:蠟料從加工溫度(如70℃)冷卻至室溫(如20℃)時(shí),因熱脹冷縮效應(yīng)產(chǎn)生體積收縮。例如,石蠟基中溫蠟的線收縮率通常為0.8%~1.2%,合成蠟基材料可能更高(可達(dá)1.5%)。
相變收縮:蠟料從液態(tài)凝固為固態(tài)時(shí),分子排列致密化導(dǎo)致體積進(jìn)一步收縮(占總收縮量的30%~50%)。
收縮過程具有階段性:
液態(tài)冷卻階段(加工溫度→凝固點(diǎn)):以熱收縮為主,速度較快;
固態(tài)冷卻階段(凝固點(diǎn)→室溫):熱收縮與相變收縮疊加,收縮量占比約60%~70%。
二、對(duì)鑄件精度的具體影響
1.尺寸偏差
線性收縮:蠟?zāi)5木€收縮率直接決定鑄件的終尺寸。若蠟?zāi)J湛s率未準(zhǔn)確計(jì)算,鑄件可能出現(xiàn)整體尺寸偏小(如蠟?zāi)J湛s率預(yù)估為1.0%,實(shí)際為1.2%時(shí),鑄件關(guān)鍵尺寸偏差可達(dá)0.2%)。
不均勻收縮:
壁厚差異:厚壁區(qū)域冷卻慢,收縮量大于薄壁(如壁厚5mm的蠟?zāi)^(qū)域收縮率比壁厚2mm區(qū)域高0.3%~0.5%),導(dǎo)致鑄件壁厚不均。
結(jié)構(gòu)復(fù)雜度:復(fù)雜件因冷卻路徑不一致,易出現(xiàn)局部收縮異常(如凸臺(tái)、筋板處收縮率比平面高0.1%~0.2%)。
2.形狀畸變
應(yīng)力集中:蠟?zāi)@鋮s時(shí)若內(nèi)部應(yīng)力釋放不均,可能產(chǎn)生彎曲、扭曲等變形。例如,長(zhǎng)條形蠟?zāi)#ㄈ巛S類)若兩側(cè)冷卻速度不一致,可能向冷卻慢的一側(cè)彎曲,導(dǎo)致鑄件直線度超差。
分型面錯(cuò)位:收縮應(yīng)力可能導(dǎo)致壓型(模具)分型面處蠟料位移,形成飛邊或尺寸錯(cuò)位(如分型面處尺寸偏差±0.1mm)。
3.表面缺陷
縮孔與凹陷:蠟料收縮未能及時(shí)補(bǔ)料時(shí),厚壁中心或筋板根部易形成縮孔(直徑0.5~2mm)或表面凹陷,鑄件對(duì)應(yīng)位置會(huì)殘留孔洞或不平整。
冷隔與流痕:收縮導(dǎo)致蠟料流動(dòng)末端補(bǔ)縮不足,可能產(chǎn)生冷隔(線條狀未融合痕跡),影響鑄件表面光潔度。
三、收縮率的控制策略
1.蠟料配方優(yōu)化
添加填料:加入微粉蠟、滑石粉等填料(占比5%~10%)可降低收縮率。例如,含10%滑石粉的中溫蠟線收縮率可從1.2%降至0.9%。
選用低收縮基料:合成蠟(如聚乙烯蠟)比石蠟收縮率低(石蠟基1.0%~1.5%vs合成蠟基0.6%~1.0%),適合高精度鑄件。
2.工藝參數(shù)調(diào)整
控制冷卻速度:
快速冷卻:通過低溫壓型(如金屬模通冷卻水至20℃)或噴霧冷卻,縮短液態(tài)停留時(shí)間,減少熱收縮(線收縮率可降低0.1%~0.3%)。
緩慢冷卻:對(duì)于復(fù)雜件,采用恒溫冷卻箱(如40℃保溫2小時(shí)),使蠟料均勻收縮,減少應(yīng)力變形。
優(yōu)化壓注工藝:
提高壓力:從0.3MPa增至0.5MPa,可通過外力補(bǔ)縮減少收縮缺陷(尤其適用于厚壁件)。
分段壓注:先低壓(0.2MPa)填充型腔,再高壓(0.6MPa)保壓補(bǔ)縮,降低縮孔風(fēng)險(xiǎn)。
3.模具設(shè)計(jì)補(bǔ)償
收縮率預(yù)留:根據(jù)蠟料實(shí)測(cè)收縮率,在模具設(shè)計(jì)時(shí)放大尺寸。例如,若蠟?zāi)J湛s率為1.1%,模具尺寸需比鑄件名義尺寸大1.1%(如鑄件要求φ50mm,模具型腔設(shè)計(jì)為φ50.55mm)。
結(jié)構(gòu)改良:
在厚壁處設(shè)計(jì)工藝?yán)呋驕p薄區(qū),平衡冷卻速度;
復(fù)雜件采用組合式壓型,避免單一模具因收縮應(yīng)力導(dǎo)致變形。
4.過程監(jiān)控與修正
首件檢測(cè):通過三坐標(biāo)測(cè)量?jī)x檢測(cè)蠟?zāi)jP(guān)鍵尺寸,對(duì)比理論收縮率,及時(shí)修正模具或工藝參數(shù)(如發(fā)現(xiàn)某尺寸收縮率比預(yù)期高0.2%,下次生產(chǎn)時(shí)模具相應(yīng)部位放大0.2%)。
批次跟蹤:不同批次蠟料收縮率可能波動(dòng)(如±0.1%),投產(chǎn)前需通過試模確認(rèn)實(shí)際收縮數(shù)據(jù)。
四、典型案例分析
案例1:航空葉片蠟?zāi)W冃?br /> 問題:葉片蠟?zāi)>壈逄幨湛s變形,導(dǎo)致鑄件緣板厚度偏差超±0.05mm。
原因:緣板厚2.5mm,葉身厚1.2mm,冷卻速度差異導(dǎo)致應(yīng)力集中。
解決:壓型緣板區(qū)域嵌入銅質(zhì)冷卻塊(導(dǎo)熱率提高3倍),使緣板與葉身冷卻速度接近,收縮率差異從0.4%降至0.1%,鑄件精度達(dá)標(biāo)。
案例2:齒輪箱蠟?zāi)?s孔
問題:蠟?zāi)]S承座孔內(nèi)出現(xiàn)φ1mm縮孔,鑄件機(jī)加工后暴露。
原因:軸承座孔壁厚8mm,蠟料收縮時(shí)補(bǔ)料不足。
解決:壓注時(shí)增加頂針補(bǔ)料機(jī)構(gòu)(在孔中心設(shè)置可移動(dòng)頂針,冷卻過程中持續(xù)注入熱蠟料),縮孔消除,鑄件合格率從75%提升至98%。
中溫蠟收縮率對(duì)鑄件精度的影響具有累積性和隱蔽性,需從蠟料選擇、工藝設(shè)計(jì)到生產(chǎn)監(jiān)控全流程管控。通過精確測(cè)量收縮率數(shù)據(jù)(建議每批次蠟料實(shí)測(cè)3組以上)、模具動(dòng)態(tài)補(bǔ)償及冷卻路徑優(yōu)化,可將收縮導(dǎo)致的尺寸偏差控制在±0.03mm以內(nèi),滿足航空航天、精密機(jī)械等高精度鑄件需求。實(shí)際生產(chǎn)中,建議建立“蠟料收縮率-工藝參數(shù)-鑄件精度”關(guān)聯(lián)數(shù)據(jù)庫(kù),實(shí)現(xiàn)快速工藝匹配與問題追溯。
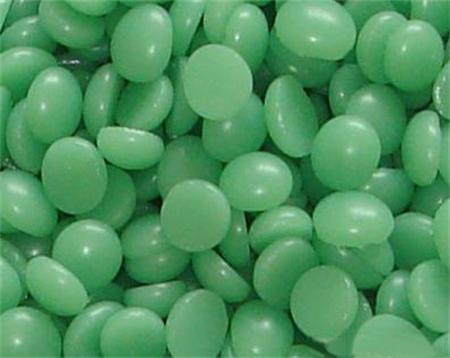