中溫蠟的加工溫度范圍如何確定?
發布日期:2025-05-07 00:00 來源://sdtxblg.com 點擊:
中溫蠟的加工溫度范圍需綜合考慮蠟料特性、鑄件結構、工藝要求及設備性能等多方面因素,通過理論分析與實踐調試確定。以下是具體依據和方法:
一、核心影響因素
蠟料的物理特性
熔點與軟化點:中溫蠟的熔點通常在50~80℃(不同配方略有差異),軟化點一般比熔點低5~10℃。加工溫度需高于軟化點以保證流動性,同時避免超過熱分解溫度(通常不超過90℃,否則蠟料易碳化、發煙)。
粘度與流動性:溫度升高時蠟料粘度降低、流動性增強,但溫度過高會導致蠟料收縮率增大、表面粗糙度變差。需通過試驗找到粘度-溫度曲線的更佳區間(如某石蠟基中溫蠟在65~75℃時粘度穩定在50~100mPa?s,適合復雜件成型)。
鑄件結構與尺寸
復雜薄壁件:需更高的溫度以提升蠟料流動性,確保型腔填充完整(如溫度可設定在70~80℃)。
厚壁或簡單件:可適當降低溫度以減少收縮缺陷(如60~70℃),避免高溫下蠟料過度流動導致尺寸偏差。
制模工藝要求
壓型溫度:模具(壓型)的溫度會影響蠟料冷卻速度。若壓型為金屬材質且溫度較低(如20~30℃),蠟料溫度需適當提高(如75~80℃)以補償熱量損失;若壓型預熱(如40~50℃),蠟料溫度可降低5~10℃。
壓制壓力:低壓制模(如手動壓注)時需更高溫度提升流動性;高壓制模(如機械壓注)可適當降低溫度,利用壓力保證填充(如壓力每增加1MPa,溫度可降低2~3℃)。
環境條件
室溫與濕度:低溫環境(如冬季室溫<15℃)會加速蠟料冷卻,需提高加工溫度5~10℃;高溫高濕環境(如夏季)需防止蠟料過熱,溫度可控制在中下限(如65~70℃)。
二、確定溫度范圍的步驟
參考蠟料供應商建議
每種中溫蠟(如石蠟-硬脂酸基、合成蠟基)均有廠家推薦的標準溫度區間(例如某品牌中溫蠟建議為68~78℃),可作為初始調試依據。
單因素試驗法
固定其他變量(如壓型溫度、壓力、鑄件類型),僅改變蠟料溫度,觀察以下指標:
充型完整性:低溫下是否出現缺料、棱角不清;高溫下是否產生飛邊、表面氣泡。
尺寸精度:測量蠟模關鍵尺寸,對比不同溫度下的收縮率(如溫度每升高5℃,線收縮率可能增加0.1%~0.3%)。
表面質量:高溫下蠟模表面是否光滑,低溫下是否有冷隔、橘皮紋。
記錄合格蠟模對應的溫度范圍(如某工況下65~75℃為可行區間)。
多因素綜合調試
結合壓型溫度、壓力等變量進行正交試驗。例如:
當壓型溫度為30℃、壓力為0.3MPa時,蠟料溫度68~75℃為更佳;
若壓型溫度升至40℃、壓力增至0.5MPa,溫度可下調至63~70℃。
極限驗證
測試溫度上限:加熱蠟料至開始冒煙或出現異味(接近熱分解溫度),實際使用溫度需低于該值5~10℃。
測試溫度下限:逐步降低溫度直至蠟料無法充滿型腔,實際使用溫度需高于該值5~10℃。
三、溫度控制要點
加熱設備精度
使用帶溫控儀的專用蠟料保溫罐或水浴鍋,溫控精度需達到±1℃,避免局部過熱或溫度波動過大。
溫度均勻性
蠟料加熱時需持續攪拌(如磁力攪拌或低速機械攪拌),防止底部或邊緣過熱碳化。
實時監測
用接觸式溫度計(如熱電偶)直接測量蠟料熔體溫度,避免依賴設備顯示溫度(可能存在滯后或誤差)。
批次差異調整
不同批次蠟料因原料波動可能導致溫度范圍偏移,新批次使用前需重新調試(如同一型號蠟料,A批次更佳溫度為67~76℃,B批次可能為65~74℃)。
四、常見問題與溫度關聯分析
問題1:蠟模表面粗糙、有針孔
可能原因:溫度過低導致蠟料流動不暢,卷入空氣;或溫度過高使蠟料熱分解產生氣體。
解決:提高溫度5~8℃(若原溫度偏低)或降低3~5℃(若原溫度偏高),并延長攪拌除氣時間。
問題2:蠟模尺寸超差(收縮過大)
可能原因:溫度過高導致冷卻時收縮量增加。
解決:降低溫度至中下限,或加快壓型冷卻速度(如通入冷卻水)。
問題3:充型不滿、邊角缺料
可能原因:溫度過低或壓力不足。
解決:提高溫度3~5℃,同時檢查壓制壓力是否達到工藝要求(如是否從0.2MPa提升至0.3MPa)。
通過系統分析蠟料特性、工藝條件及實際測試,可精準確定中溫蠟的加工溫度范圍。實際生產中建議采用“分段控溫”策略(如粗加工用上限溫度保證效率,精加工用下限溫度保證精度),并建立溫度-工藝參數對應表,以實現穩定批量生產。
一、核心影響因素
蠟料的物理特性
熔點與軟化點:中溫蠟的熔點通常在50~80℃(不同配方略有差異),軟化點一般比熔點低5~10℃。加工溫度需高于軟化點以保證流動性,同時避免超過熱分解溫度(通常不超過90℃,否則蠟料易碳化、發煙)。
粘度與流動性:溫度升高時蠟料粘度降低、流動性增強,但溫度過高會導致蠟料收縮率增大、表面粗糙度變差。需通過試驗找到粘度-溫度曲線的更佳區間(如某石蠟基中溫蠟在65~75℃時粘度穩定在50~100mPa?s,適合復雜件成型)。
鑄件結構與尺寸
復雜薄壁件:需更高的溫度以提升蠟料流動性,確保型腔填充完整(如溫度可設定在70~80℃)。
厚壁或簡單件:可適當降低溫度以減少收縮缺陷(如60~70℃),避免高溫下蠟料過度流動導致尺寸偏差。
制模工藝要求
壓型溫度:模具(壓型)的溫度會影響蠟料冷卻速度。若壓型為金屬材質且溫度較低(如20~30℃),蠟料溫度需適當提高(如75~80℃)以補償熱量損失;若壓型預熱(如40~50℃),蠟料溫度可降低5~10℃。
壓制壓力:低壓制模(如手動壓注)時需更高溫度提升流動性;高壓制模(如機械壓注)可適當降低溫度,利用壓力保證填充(如壓力每增加1MPa,溫度可降低2~3℃)。
環境條件
室溫與濕度:低溫環境(如冬季室溫<15℃)會加速蠟料冷卻,需提高加工溫度5~10℃;高溫高濕環境(如夏季)需防止蠟料過熱,溫度可控制在中下限(如65~70℃)。
二、確定溫度范圍的步驟
參考蠟料供應商建議
每種中溫蠟(如石蠟-硬脂酸基、合成蠟基)均有廠家推薦的標準溫度區間(例如某品牌中溫蠟建議為68~78℃),可作為初始調試依據。
單因素試驗法
固定其他變量(如壓型溫度、壓力、鑄件類型),僅改變蠟料溫度,觀察以下指標:
充型完整性:低溫下是否出現缺料、棱角不清;高溫下是否產生飛邊、表面氣泡。
尺寸精度:測量蠟模關鍵尺寸,對比不同溫度下的收縮率(如溫度每升高5℃,線收縮率可能增加0.1%~0.3%)。
表面質量:高溫下蠟模表面是否光滑,低溫下是否有冷隔、橘皮紋。
記錄合格蠟模對應的溫度范圍(如某工況下65~75℃為可行區間)。
多因素綜合調試
結合壓型溫度、壓力等變量進行正交試驗。例如:
當壓型溫度為30℃、壓力為0.3MPa時,蠟料溫度68~75℃為更佳;
若壓型溫度升至40℃、壓力增至0.5MPa,溫度可下調至63~70℃。
極限驗證
測試溫度上限:加熱蠟料至開始冒煙或出現異味(接近熱分解溫度),實際使用溫度需低于該值5~10℃。
測試溫度下限:逐步降低溫度直至蠟料無法充滿型腔,實際使用溫度需高于該值5~10℃。
三、溫度控制要點
加熱設備精度
使用帶溫控儀的專用蠟料保溫罐或水浴鍋,溫控精度需達到±1℃,避免局部過熱或溫度波動過大。
溫度均勻性
蠟料加熱時需持續攪拌(如磁力攪拌或低速機械攪拌),防止底部或邊緣過熱碳化。
實時監測
用接觸式溫度計(如熱電偶)直接測量蠟料熔體溫度,避免依賴設備顯示溫度(可能存在滯后或誤差)。
批次差異調整
不同批次蠟料因原料波動可能導致溫度范圍偏移,新批次使用前需重新調試(如同一型號蠟料,A批次更佳溫度為67~76℃,B批次可能為65~74℃)。
四、常見問題與溫度關聯分析
問題1:蠟模表面粗糙、有針孔
可能原因:溫度過低導致蠟料流動不暢,卷入空氣;或溫度過高使蠟料熱分解產生氣體。
解決:提高溫度5~8℃(若原溫度偏低)或降低3~5℃(若原溫度偏高),并延長攪拌除氣時間。
問題2:蠟模尺寸超差(收縮過大)
可能原因:溫度過高導致冷卻時收縮量增加。
解決:降低溫度至中下限,或加快壓型冷卻速度(如通入冷卻水)。
問題3:充型不滿、邊角缺料
可能原因:溫度過低或壓力不足。
解決:提高溫度3~5℃,同時檢查壓制壓力是否達到工藝要求(如是否從0.2MPa提升至0.3MPa)。
通過系統分析蠟料特性、工藝條件及實際測試,可精準確定中溫蠟的加工溫度范圍。實際生產中建議采用“分段控溫”策略(如粗加工用上限溫度保證效率,精加工用下限溫度保證精度),并建立溫度-工藝參數對應表,以實現穩定批量生產。
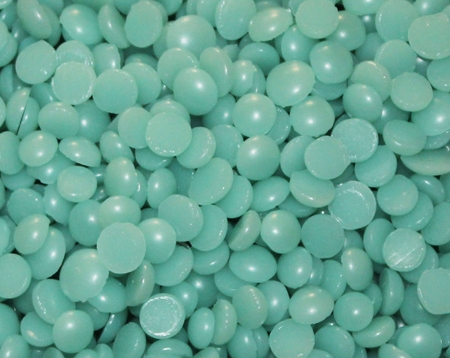