精鑄蠟的收縮率如何控制?
發布日期:2025-06-23 00:00 來源://sdtxblg.com 點擊:
精密鑄造(也稱失蠟鑄造)是一種廣泛應用于航空航天、汽車、醫療器械等領域的制造工藝。精鑄蠟作為該工藝中的關鍵材料,其收縮率直接影響到終鑄件的尺寸精度和表面質量。因此,控制精鑄蠟的收縮率是確保鑄件質量的重要環節。本文將從精鑄蠟的材料特性、工藝參數、模具設計以及后處理等方面,詳細探討如何有效控制精鑄蠟的收縮率。
一、精鑄蠟的材料特性
精鑄蠟的收縮率與其材料特性密切相關。常見的精鑄蠟主要由石蠟、微晶蠟、聚乙烯蠟等組成,不同的蠟料配方會導致不同的收縮率。以下是一些影響收縮率的關鍵因素:
蠟料的成分:不同種類的蠟料具有不同的熱膨脹系數和冷卻速率。例如,石蠟的收縮率較高,而聚乙烯蠟的收縮率較低。通過調整蠟料中各組分的比例,可以有效控制整體收縮率。
蠟料的純度:雜質的存在會影響蠟料的均勻性和冷卻速率,進而影響收縮率。因此,選擇高純度的蠟料是控制收縮率的基礎。
蠟料的熔點和凝固點:蠟料的熔點和凝固點決定了其在冷卻過程中的收縮行為。通常,熔點較高的蠟料在冷卻過程中收縮率較大。因此,選擇合適的熔點和凝固點有助于控制收縮率。
二、工藝參數的控制
在精鑄蠟的制備和使用過程中,工藝參數的設置對收縮率有顯著影響。以下是一些關鍵的工藝參數及其控制方法:
注蠟溫度:注蠟溫度過高會導致蠟料流動性過強,冷卻過程中收縮率增大;注蠟溫度過低則可能導致蠟料填充不充分,影響蠟模的完整性。因此,選擇合適的注蠟溫度是控制收縮率的關鍵。通常,注蠟溫度應略高于蠟料的熔點,以確保蠟料具有良好的流動性,同時避免過熱。
注蠟壓力:注蠟壓力的大小直接影響蠟料的填充效果和冷卻過程中的收縮行為。過高的注蠟壓力可能導致蠟料在模具中產生內應力,冷卻后收縮率增大;過低的注蠟壓力則可能導致蠟料填充不充分。因此,應根據蠟料的特性和模具結構,選擇合適的注蠟壓力。
冷卻速率:蠟料的冷卻速率對收縮率有重要影響。快速冷卻會導致蠟料內部產生較大的內應力,增加收縮率;而緩慢冷卻則有助于減少內應力,降低收縮率。因此,控制冷卻速率是控制收縮率的重要手段。可以通過調整冷卻介質的溫度、冷卻時間等參數,實現冷卻速率的控制。
三、模具設計
模具設計對精鑄蠟的收縮率也有重要影響。合理的模具設計可以有效減少蠟料在冷卻過程中的收縮,提高鑄件的尺寸精度。以下是一些模具設計中的關鍵點:
模具的收縮補償:在設計模具時,應考慮蠟料的收縮率,并在模具尺寸上進行相應的補償。例如,如果蠟料的收縮率為1%,則模具的尺寸應比終鑄件的尺寸大1%,以補償蠟料在冷卻過程中的收縮。
模具的冷卻系統:模具的冷卻系統設計對蠟料的冷卻速率有重要影響。合理的冷卻系統設計可以確保蠟料在模具中均勻冷卻,減少內應力的產生,從而降低收縮率。可以通過在模具中設置冷卻水道、使用冷卻介質等方式,實現均勻冷卻。
模具的表面處理:模具的表面粗糙度對蠟料的填充和冷卻過程有影響。表面過于粗糙的模具可能導致蠟料在填充過程中產生氣泡或缺陷,增加收縮率。因此,模具表面應進行適當的拋光處理,以確保蠟料的順利填充和均勻冷卻。
四、后處理
在蠟模制備完成后,適當的后處理也有助于控制收縮率。以下是一些常見的后處理方法:
蠟模的穩定化處理:蠟模在冷卻后可能存在一定的內應力,導致后續的收縮。通過將蠟模在一定溫度下進行穩定化處理,可以消除內應力,減少后續的收縮率。穩定化處理的溫度和時間應根據蠟料的特性進行選擇。
蠟模的修整:蠟模在冷卻后可能產生一些小的缺陷或變形,通過適當的修整可以確保蠟模的尺寸精度和表面質量。修整過程中應注意避免對蠟模造成新的內應力,以免增加收縮率。
蠟模的儲存:蠟模在儲存過程中可能會受到環境溫度的影響,導致進一步的收縮。因此,蠟模應儲存在恒溫、恒濕的環境中,以避免因環境變化導致的收縮。
控制精鑄蠟的收縮率是確保精密鑄件質量的關鍵環節。通過合理選擇蠟料、控制工藝參數、優化模具設計以及進行適當的后處理,可以有效降低精鑄蠟的收縮率,提高鑄件的尺寸精度和表面質量。在實際生產中,應根據具體的工藝條件和產品要求,綜合考慮上述因素,制定合理的控制方案,以實現更佳的生產效果。
精鑄蠟的收縮率控制是一個系統工程,需要從材料、工藝、模具和后處理等多個方面進行綜合考慮。只有通過科學的分析和精細的操作,才能確保精鑄蠟的收縮率得到有效控制,終生產出高質量的精密鑄件。
一、精鑄蠟的材料特性
精鑄蠟的收縮率與其材料特性密切相關。常見的精鑄蠟主要由石蠟、微晶蠟、聚乙烯蠟等組成,不同的蠟料配方會導致不同的收縮率。以下是一些影響收縮率的關鍵因素:
蠟料的成分:不同種類的蠟料具有不同的熱膨脹系數和冷卻速率。例如,石蠟的收縮率較高,而聚乙烯蠟的收縮率較低。通過調整蠟料中各組分的比例,可以有效控制整體收縮率。
蠟料的純度:雜質的存在會影響蠟料的均勻性和冷卻速率,進而影響收縮率。因此,選擇高純度的蠟料是控制收縮率的基礎。
蠟料的熔點和凝固點:蠟料的熔點和凝固點決定了其在冷卻過程中的收縮行為。通常,熔點較高的蠟料在冷卻過程中收縮率較大。因此,選擇合適的熔點和凝固點有助于控制收縮率。
二、工藝參數的控制
在精鑄蠟的制備和使用過程中,工藝參數的設置對收縮率有顯著影響。以下是一些關鍵的工藝參數及其控制方法:
注蠟溫度:注蠟溫度過高會導致蠟料流動性過強,冷卻過程中收縮率增大;注蠟溫度過低則可能導致蠟料填充不充分,影響蠟模的完整性。因此,選擇合適的注蠟溫度是控制收縮率的關鍵。通常,注蠟溫度應略高于蠟料的熔點,以確保蠟料具有良好的流動性,同時避免過熱。
注蠟壓力:注蠟壓力的大小直接影響蠟料的填充效果和冷卻過程中的收縮行為。過高的注蠟壓力可能導致蠟料在模具中產生內應力,冷卻后收縮率增大;過低的注蠟壓力則可能導致蠟料填充不充分。因此,應根據蠟料的特性和模具結構,選擇合適的注蠟壓力。
冷卻速率:蠟料的冷卻速率對收縮率有重要影響。快速冷卻會導致蠟料內部產生較大的內應力,增加收縮率;而緩慢冷卻則有助于減少內應力,降低收縮率。因此,控制冷卻速率是控制收縮率的重要手段。可以通過調整冷卻介質的溫度、冷卻時間等參數,實現冷卻速率的控制。
三、模具設計
模具設計對精鑄蠟的收縮率也有重要影響。合理的模具設計可以有效減少蠟料在冷卻過程中的收縮,提高鑄件的尺寸精度。以下是一些模具設計中的關鍵點:
模具的收縮補償:在設計模具時,應考慮蠟料的收縮率,并在模具尺寸上進行相應的補償。例如,如果蠟料的收縮率為1%,則模具的尺寸應比終鑄件的尺寸大1%,以補償蠟料在冷卻過程中的收縮。
模具的冷卻系統:模具的冷卻系統設計對蠟料的冷卻速率有重要影響。合理的冷卻系統設計可以確保蠟料在模具中均勻冷卻,減少內應力的產生,從而降低收縮率。可以通過在模具中設置冷卻水道、使用冷卻介質等方式,實現均勻冷卻。
模具的表面處理:模具的表面粗糙度對蠟料的填充和冷卻過程有影響。表面過于粗糙的模具可能導致蠟料在填充過程中產生氣泡或缺陷,增加收縮率。因此,模具表面應進行適當的拋光處理,以確保蠟料的順利填充和均勻冷卻。
四、后處理
在蠟模制備完成后,適當的后處理也有助于控制收縮率。以下是一些常見的后處理方法:
蠟模的穩定化處理:蠟模在冷卻后可能存在一定的內應力,導致后續的收縮。通過將蠟模在一定溫度下進行穩定化處理,可以消除內應力,減少后續的收縮率。穩定化處理的溫度和時間應根據蠟料的特性進行選擇。
蠟模的修整:蠟模在冷卻后可能產生一些小的缺陷或變形,通過適當的修整可以確保蠟模的尺寸精度和表面質量。修整過程中應注意避免對蠟模造成新的內應力,以免增加收縮率。
蠟模的儲存:蠟模在儲存過程中可能會受到環境溫度的影響,導致進一步的收縮。因此,蠟模應儲存在恒溫、恒濕的環境中,以避免因環境變化導致的收縮。
控制精鑄蠟的收縮率是確保精密鑄件質量的關鍵環節。通過合理選擇蠟料、控制工藝參數、優化模具設計以及進行適當的后處理,可以有效降低精鑄蠟的收縮率,提高鑄件的尺寸精度和表面質量。在實際生產中,應根據具體的工藝條件和產品要求,綜合考慮上述因素,制定合理的控制方案,以實現更佳的生產效果。
精鑄蠟的收縮率控制是一個系統工程,需要從材料、工藝、模具和后處理等多個方面進行綜合考慮。只有通過科學的分析和精細的操作,才能確保精鑄蠟的收縮率得到有效控制,終生產出高質量的精密鑄件。
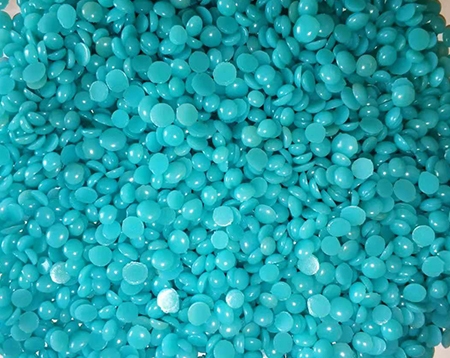